The flexographic ink delivery process has come a long way since the days when “Fragile – Do Not Drop” and “This End Up” were the only requirements of box printers. New press designs are able to achieve the quality of work that has traditionally been done by litho lamination, and corrugated printers have to produce a consistently high level of quality to compete. The evolution of the ink delivery process from a two-roll ink metering system to the enclosed doctor blade chamber has made this possible.
There are currently three types of ink metering systems used in corrugated printing applications: the two-roll system, the single blade system and the enclosed doctor blade chamber system. All three systems rely on an anilox roll to transfer ink to the plate. The difference lies in how the ink is applied to the anilox roll.
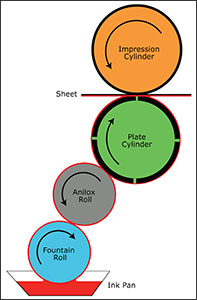
The Two-Roll Ink Delivery System
In the original two-roll ink metering system, a fountain roll rotates partially submerged in an open ink pan, picking up ink and applying it to the anilox roll. The anilox roll transfers the ink to the plate cylinder which then lays it down on the sheet. Though still widely used in the industry, there is a lot of variability in the two-roll system which results in a lack of control over the amount of ink transferred to the plate:
- Imprecise wipe of the anilox roll leads to inconsistent volume of ink delivered to the sheet.
- Color strength fluctuation and ink slinging can occur at higher press speeds due to the hydraulic force between the rubber roll and the anilox roll.
- Transfer characteristics vary according to the hardness or “durometer” of the rubber roll.
- Ink viscosity is subject to evaporation, dust and surface skimming due to the open tray design.
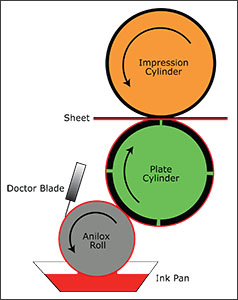
Single Doctor Blade Ink Delivery System
The addition of a reverse angle doctor blade added precision to the ink metering process. In the single blade ink metering system, a doctor blade made from steel, plastic or a composite material is used to replace the rubber roll. The blade is installed just beyond the ink metering nip to shear ink from the anilox roll surface. Doctor blade ink metering systems give the printer better control over the volume of ink being delivered to the plate. Where a rubber roll often leaves an additional ink film on the surface, a doctor blade shears ink cleanly from the roll. The inks perform better on press and a printer can achieve a more consistent ink film thickness. Ink consumption is reduced, and color application is consistent across the sheet even at higher press speeds.
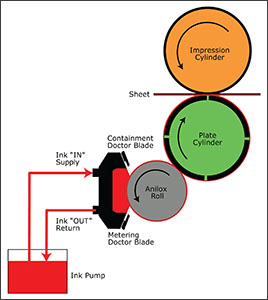
Enclosed Chamber Doctor Blade System
The most recent development in the flexographic inking process is the enclosed chamber doctor blade system. In this system, two doctor blades are used along with an enclosed chamber to dispense the ink to the anilox roll. The reverse angle blade acts as the metering blade and wipes excess ink from the anilox roll. The trailing blade acts as a capture or containment blade and holds the ink within the chamber. Foam, rubber or felt gaskets seal both ends of the chamber and keep ink from leaking out. The ink is delivered through a closed loop from the ink pump to the doctor blade system and then back to the pump.
With this method, a printer can maintain ink viscosity because the enclosed design provides protection from evaporation of solvents or amines from the ink, depending on whether the ink is solvent or water-based. Also, dust, slinging and skimming are minimized. Better control over ink usage means lower ink consumption by as much as 15% per year. The system holds less ink than open pans, so there is not as much leftover ink at the end of a press run and ink can be removed and stored for future use.
Due to a more efficient cleaning process, a smaller amount of cleaning solution is needed to clean up a chamber so cleaning solution waste and disposal costs are also reduced. Color changes are quick, speeding up changeover and setup time on a run. The enclosed chamber system is more eco-friendly because of reduced ink consumption and disposal of waste ink as well as a lower volume of cleaning solution and water required to wash-up the station for a color change.
After years of being relegated to jobs with low graphics requirements, flexography now rivals other printing methods for quality. Today’s corrugated printers are able to produce products that are highly attractive and eye-catching to the consumer due to advances in the ink delivery process. Whether they opt for a single doctor blade system or see the benefits in investing in a dual blade enclosed chamber, printers gain clear advantages by using doctor blades in terms of controlling ink film thickness and maintaining color consistency.