In flexographic printing, perfect print quality and efficiency are the ultimate goals for press operators. One pesky obstacle that often disrupts this quest is the notorious “back doctoring” or “trail doctoring.”
Understanding Back Doctoring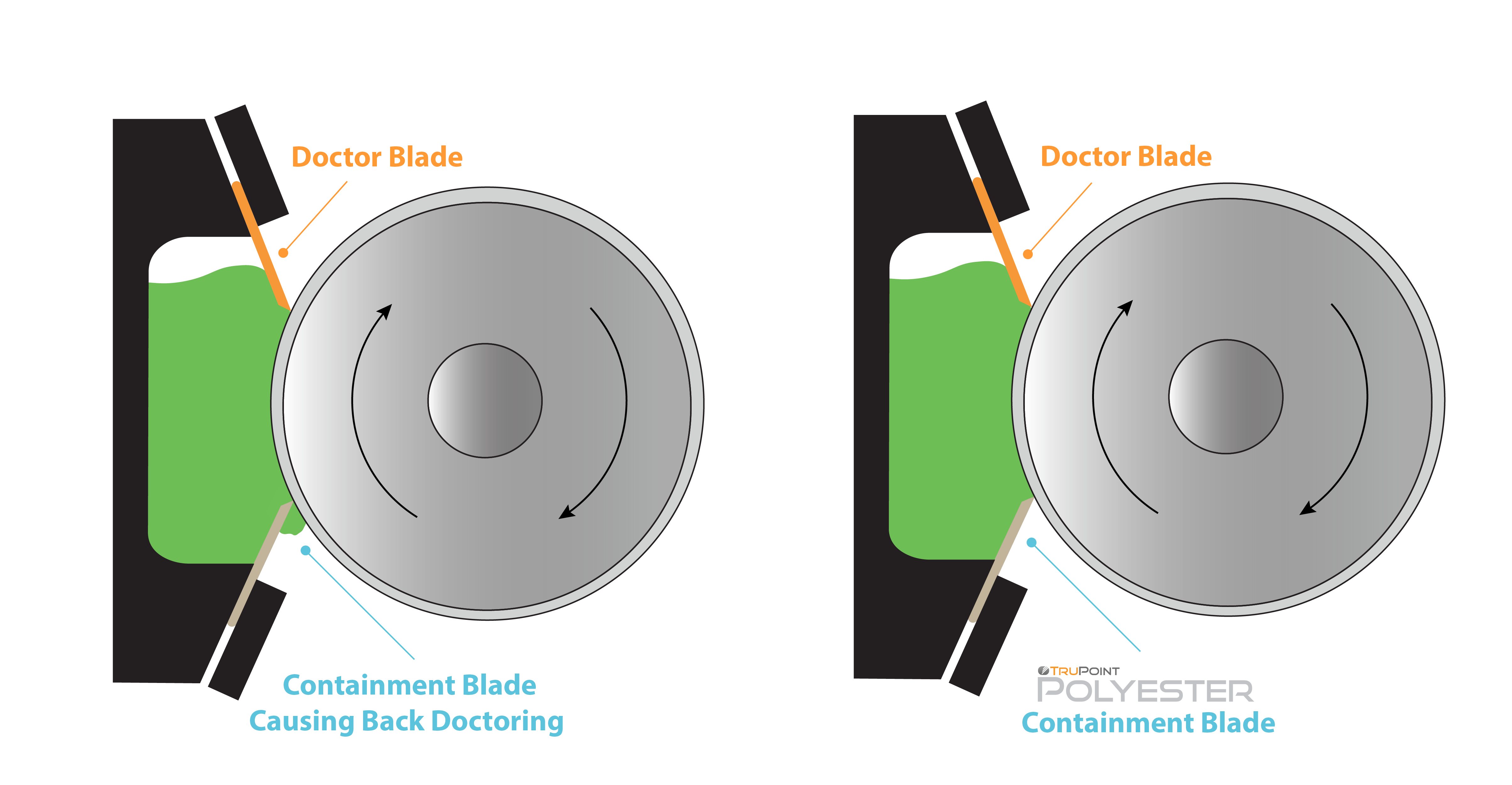
No press operator wants to deal with the hassle of frequent press stoppages for cleaning sessions. Back doctoring or trail doctoring, is not only a nuisance but also a costly problem, leading to lost press time, wasted ink, and substrate.
Doctor Blade vs Containment Blade
The doctor blade and containment blade play different roles in transferring ink from the anilox roll to the substrate. Choose each blade carefully to ensure the doctor blade chamber works optimally.
Doctor blades ensure precise ink transfer to the printing plate and substrate. It meters ink from the anilox roll before the transfer takes place. The doctor blade needs to be stiff and rigid to prevent ink from passing underneath it, leading to excess ink on the anilox roll.
Conversely, the containment blade collects any excess ink post-transfer. The rotation of the anilox roll lifts the tip of the containment blade, allowing ink to flow underneath. The ink flows back into the chamber, reclaiming it for future use. Unlike the doctor blade, the containment blade should be thin and flexible to create a one-way “valve.”
Back Doctoring Explained
Back doctoring occurs when the containment blade meters or doctors the ink, preventing its return to the chamber. The primary culprit of back doctoring is a steel containment blade. Due to its stiffness, steel doctor blades prohibit ink from re-entering the ink chamber on the back side of the anilox roll. Back doctoring can also occur when operating at high speeds or with smaller anilox diameters. The centrifugal force of the roll as it turns is greater causing the containment blade to become ineffective.
Defeat Back Doctoring
The key to eliminating back doctoring is using the right containment blade.
The containment blade should be thin and flexible so the rotation of the anilox roll can lift it. This allows the containment blade to effectively remove excess ink and create a one-way path for it to return to its chamber. Unlike a doctor blade, a containment blade does not require a bevel to function correctly. Choosing a straight or radius blade edge will optimize performance and cost.
Polyester containment blades offer a winning combination of flexibility, stability, and solvent resistance. Not only are they more cost-effective than steel doctor blades, but they also enhance safety during the printing process. With no sharp fragments to worry about, polyester blades reduce anilox roll scoring and excessive wear.
Back doctoring is a common pressroom problem that, fortunately, has an easy fix: converting to a polyester containment blade. Choosing a plastic blade keeps unused ink in the chamber reducing downtime and increasing print efficiency – even at high press speeds.
Read our blog post, “5 Reasons to Switch to Polyester Containment Blades” to learn more about the benefits of using high-performance polyester containment blades.